As part of a class project (MECH 3350: Kinematics and Dynamics of Mechanical Systems), my team and I were tasked to develop a linkage to solve a relevant engineering problem. We decided to design a mechanism to control a slotted flap of an aircraft, taking into account the effect of different flap positions, and ensuring that the mechanism could be adequately fastened to the main body of the wing. CFD simulations were performed to ensure that the various locations and angles of the flap would produce the desired lift and drag.
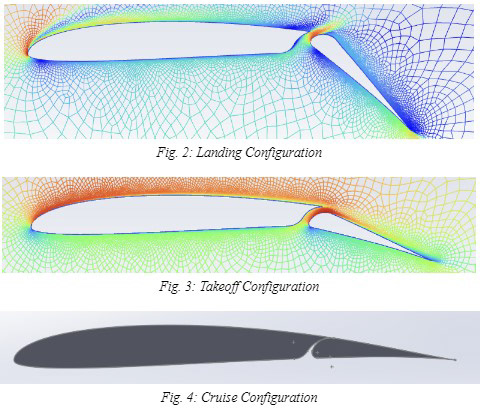
Once the desired locations of the flap had been determined from the CFD, I used SOLIDWORKS to synthesize the mechanism. Constrained by the fact that the grounded pivots of the mechanism had to be located on our airfoil, I re-ran the synthesis process multiple times before arriving at a solution that controlled the flap correctly without affecting the aerodynamics of the wing. Below you can see the final mechanism design, complete with all three positions, as demonstrated above. You can also see the animated output of a MATLAB script that we wrote as a team, that clearly shows the desired motion of the linkage between the points of interest.
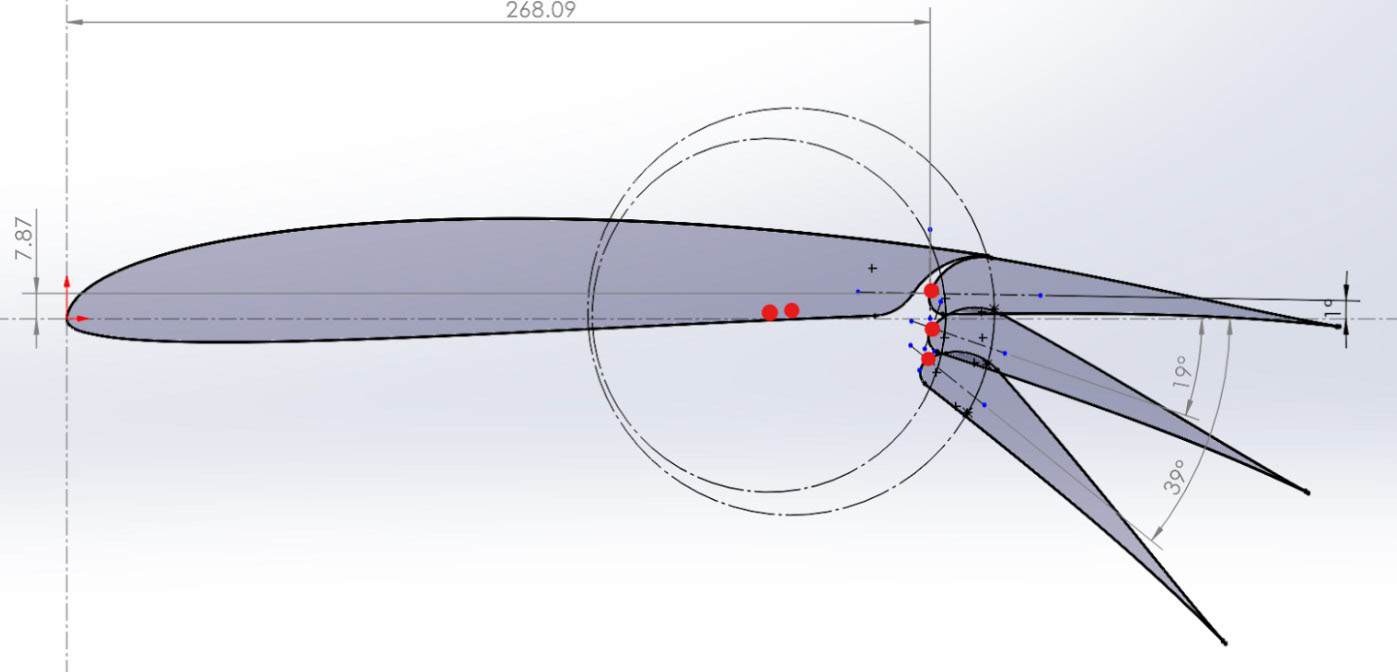
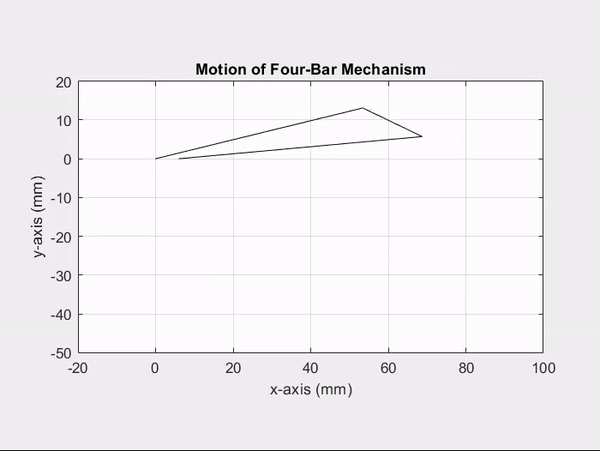
At the conclusion of the design process, we 3D-printed a prototype of our mechanism and I presented our design process in front of our class. Our design, manufacturing and presentation earned the entire team A+ grades.